ServicesTechnical Services
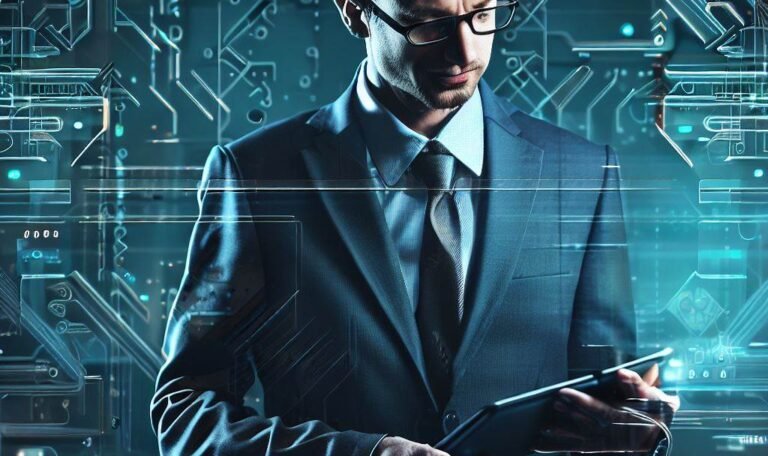
Sustainability Development
- No Poverty: “End Extreme Poverty in all forms”
- Zero Hunger: “End Hunger, Achieve Food security & improved Nutrition & Promote Sustainable Agriculture”
- Good Health & Well-being: “Ensure Healthy lives & promote well-being for all at all ages”.
- Quality Education: “Ensure inclusive & equitable quality education & promote lifelong learning opportunities for all”.
- Gender Equality: “Achieve Gender equality & empower all women & girls”
- Clean water : “Ensure availability & sustainable management of water & sanitation for all”.
- Affordable & Clean Energy : “Ensure access to affordable, reliable sustainable & modern energy for all”.
- Decent work & economic growth : “Promote sustained, inclusive & sustainable economic growth, full & productive employment & decent work for all”.
- Industry innovation & Infrastructure: “Built resilient infrastructure, promote inclusive & sustainable industrialization & foster innovation”.
- Reduced Inequalities: “Reduce inequality among countries”
- Sustainable cities & communities: “Make cities & human settlements inclusive, safe, resilient & sustainable”
- Responsible Production & Consumption: “Ensure sustainable consumption & production patterns”.
- Climate Action: “Take urgent action to combat climate change & its impacts”.
- Life below water: “Conserve & sustainably use the oceans, seas & marine resources for sustainable dev.”
- Life on land: “Protect, restore & promote sustainable use of terrestrial ecosystems, sustainably manage forests, combat desertification & halt reserve land degradation & halt biodiversity loss”
- Peace, justice & strong institutions: “Promote peaceful & inclusive societies for sustainable development, provide access to justice for all & built effective, accountable & inclusive institutions at all levels”.
- Partnerships for the goals: “Strengthen the means of implementation & revitalize the global partnership for sustainable dev.”
At ESPL, we specialize in providing comprehensive services to support organizations in their sustainability efforts. With expertise in sustainable sourcing, social responsibility, and optimizing supply chain processes, we are dedicated to helping you achieve a more responsible and resilient supply chain. Our tailored solutions and collaborative approach ensure that we address your unique needs and goals. Partner with us to unlock the benefits of a sustainable supply chain, drive positive change, and create a better future. Visit our website or contact our team to learn more about how we can assist you on your sustainability journey.


ISO Standards
- Consultancy and Gap Analysis: Offer consultancy services to assess the company’s current practices and identify areas that need improvement to meet kosher standards.
- Documentation and Process Development: Assist in developing standard operating procedures (SOPs) and documentation to ensure compliance with kosher requirements.
- Ingredient Verification: Help the company in evaluating ingredients and verifying their kosher status.
- Training and Education: Conduct training sessions for company personnel to educate them about kosher requirements and best practices.
- Auditing and Compliance Support: Prepare the company for the kosher certification audit and provide support during the certification process.
- Regulatory Knowledge: Stay updated on kosher regulations and requirements, providing insights to help the company maintain kosher compliance. ISO 9000 – Quality Management System-ISO 9000 is a family of international standards developed and published by the International Organization for Standardization (ISO). These standards focus on quality management systems (QMS) and provide guidelines and requirements to help organizations ensure they consistently meet customer requirements and enhance customer satisfaction. The ISO 9000 standards are applicable to various types of organizations, regardless of their size or industry. To support an organization in implementing ISO 9000 and achieving certification, we will-
- Gap Assessment: Conduct a gap analysis to identify the areas where your current quality management system falls short of meeting ISO 9001 requirements.
- Creation of an Implementation Plan: We will Develop a comprehensive plan that outlines the steps, responsibilities, and timelines for implementing the necessary changes to meet ISO 9001 requirements.
- Establishment of the Documentation: We will Create and maintain documentation that demonstrates how your organization meets the ISO 9001 requirements. This includes policies, procedures, work instructions, and records.
- Training and Awareness: We will ensure that all employees are aware of the ISO 9001 requirements and how they relate to their roles. Provide appropriate training to employees involved in the implementation process.
- Internal Auditing: We will Conduct internal audits to assess the effectiveness of your quality management system and identify areas for improvement.
- Corrective and Preventive Actions: Establish processes for addressing non-conformities and taking preventive actions to avoid potential issues.
- Seek External Certification: we will support in attaining the certificate from accredited certification body to provide ISO 9001 certification upon successful implementation.
- Continual Improvement: Emphasize the importance of continual improvement in your organization’s culture. Act on feedback, monitor performance, and make iterative enhancements to your QMS
ISO 14000 – Environment Management System-
The ISO 14000 family includes several standards, with the most widely known being ISO 14001:2015 – Environmental Management Systems – Requirements with guidance for use. This standard sets out the requirements for implementing an EMS, which can be applied to organizations of all types and sizes.
Here are steps to assist in the implementation process:
- Environmental Review: We will Conduct an environmental review to identify the organization’s significant environmental aspects and their impacts.
- Assemble a Team: We will Appoint a dedicated team or environmental manager responsible for overseeing the EMS implementation.
- Environmental Policy: We will Develop an environmental policy that aligns with the organization’s values and objectives.
- Awareness training for Employees: We will engage employees at all levels in the implementation process and provide awareness training on ISO 14001 and environmental management.
- Legal Compliance: We will Ensure compliance with applicable environmental laws and regulations.
- Objective Setting: We will Establish measurable environmental objectives and targets aligned with the organization’s environmental policy.
- Documentation: We will Create and maintain documentation, including procedures, work instructions, and records related to the EMS.
- Internal Auditing: We will Conduct internal audits to assess the effectiveness of the EMS and identify areas for improvement.
- Certification Support: We will Engage an accredited certification body to conduct an external audit and grant ISO 14001 certification upon successful implementation.
ISO 20400 – Sustainable procurement
ISO 20400 is an international standard that provides guidelines on sustainable procurement. The standard can be used by an organizations that intend to improve their social, economic, and environmental sustainability. It helps companies to better implement sustainability into their business models.
Here are steps to assist in the implementation process:
- Awareness & Commitment: Raise awareness among stakeholders about sustainable procurement’s importance & secure commitment from top management.
- Baseline Assessment: Assess your current procurement practices & identify areas where sustainability can be improved.
- Stakehoder Engagement: Involve key stakeholders such as suppliers, employees & customers in sustainable procurement process to gather inputs & support.
- Policy Development: Develop a sustainable procurement policy that aligns with principles & requirements of ISO 20400.
- Integration with strategy: Integrate sustainable procuremnt objectives into your organization’s overall business strategy and decision making process.
- Capacity Building: Provide trining & education to procurement staff & other relevant employees to ensure they understand & can implement sustainable procurement practices.
- Supplier evaluation: Establish criteria for evaluatinf suppliers based on their environmental, social & economic performance.
- Contract Management: Include sustainable procurement requirements in contracts & agreements with suppliers.
- Monitoring & Reporting: Implement a system to track & measure sustainable procurement performance & report progress regularly.
- Continuous Improvement: Continuously review & improve the safety management system based on performance data & feedback
ISO/IEC 17021 – Conformity Assessment- Requirements for bodies providing audits & certification of management systems
ISO/IEC 17021 is a standard that was created for assessing certification bodies (CBs) to ensure that they are competent and that they conform to all types of management systems. It gives generic requirements for such CBs performing audit and certification in the field of quality, environmental and other forms of management systems.
Here are steps to assist in the implementation process:
- Understanding ISO 17021: Familiarize yourself with the standard & its requirements for CBs to conduct management system audits.
- Accreditation & Legal Requirements: Identify the accreditation & legal requirements necessary to operate as a CB in a region or target market.
- Expertise & Competence: Establish necessary expertise & competence of personnel involved in certification process, including auditors & Technical experts (TEs).
- Documentation & Procedures: Develop a documented management system that outlines the processes & procedures for conducting audits, managing records.
- Impartiality & Independence: Ensure impartiality & independence in all certification activities to maintain the integrity & credibility of the process.
- Risk Management: Implement a risk management system to identify & address potential risks that could impact CBs operations.
- Audit Process: Define audit process including planning, conducting audits & reporting findings in accordance with ISO 17021 standard.
- Audit Reporting & Certification: Establish clear criteria for issuing certifications based on audit results & meeting relevant management system standards.
- Confidentiality & Data Protection: Implement measures to safeguard confidentiality & protect personal data obtained during certification process.
- Monitoring & Continuous Improvement: Regularly monitor the performance of CB, conducting IA & engage in continuous improvement efforts.
- Customer Satisfaction & Feedback: Gather customer feedback to ensure customer satisfaction with certification with certification process & address any concerns.
- Accreditation Body Assessment: Prepare for assessments & audits by accreditation body to demonstrate compliance with ISO 17021 & accreditation requirements.
ISO/IEC 17025- Testing & Calibration Laboratories
ISO/IEC 17025 General requirements for the competence of testing and calibration laboratories is the main ISO/IEC standard used by testing and calibration laboratories. This enables laboratories to demonstrate that they operate competently and generate valid results, thereby promoting confidence in their work both nationally and around the world. It also helps facilitate cooperation between laboratories and other bodies by generating wider acceptance of results between countries. Test reports and certificates can be accepted from one country to another without the need for further testing, which, in turn, improves international trade.
Here are steps to assist in the implementation process:
- Understanding ISO 17025: Familiarize yourself with ISO 17025 standard & its requirements for laboratory competence, impartiality & consistent operations
- Scope Definition: Determine scope of your laboratory’s testing and calibration services to identify specific requirements that apply to your operations
- Management Commitment: Obtain commitment from top management to support implementation of ISO 17025 and ensure sufficient resources are allocated.
- Gap Analysis: Conduct gap analysis to assess your laboratory’s current practices against the requirements of ISO 17025 to identify areas of improvement.
- Document Management: Develop a comprehensive set of management system documents, including policies, procedures and work instructions to guide laboratory operations.
- Competence & Training: Ensure laboratory personnel have necessary competence through training, education & experience to perform duties effectively.
- Equipment & Calibration: Establish procedures for selection, calibration and maintenance of laboratory equipment to ensure accurate & reliable results.
- Measurement Uncertainty: Assess & report measurement uncertainty associated with testing & calibration results as required by ISO 17025.
- Quality Control & Assurance: Implement processes for internal quality control & assurance to monitor and verify the validity of tests & calibration.
- Handling of Test Items: Define procedures for receipt, handling, transportation, and storage of test items to prevent damage & contamination.
- Reporting of Results: Develop procedures for communication of test & calibration results to customers, ensuring accuracy & clarity.
- Complaints & Nonconformities: Establish a system for handling customer complaints & addressing nonconformities promptly & effectively.
- Internal Audits: Conduct regulate IA to assess effectiveness of Quality Management System & identify areas of improvement.
- Management Review: Hold periodic management reviews to evaluate laboratory’s performance & determine opportunities for improvement.
- Accreditation: Consider seeking accreditation from recognized accreditation body to demonstrate compliance with ISO 17025 & enhance laboratory’s credibility.
BRCGS- Brand Reputation Compliance Global Standard
BRCGS is a consumer protection organization which sets out key quality and safety standards throughout the food manufacturing industry. BRCGS is a market-leading global brand that helps build confidence in the supply chain, offering a suite of standards where certification provides a mark of food quality, safety and responsibility. Organizations operating to BRCGS standards improve food safety, operational efficiency, commercial growth, improved profitability and broad-based innovation.
Here are steps to assist in the implementation process:
- Familiarization: Understand BRCGS standards relevant to your business. Read & review the requirements, guidelines & documentation to gain comprehensive understanding of what needs to be achieved.
- Develop Implementation Plan: Create a detailed plan outlining the actions, timelines & milestones needed to achieve BRCGS compliance. Also ensure the plan is realistic & achievable.
- Gap Analysis: Conduct Gap analysis to assess current processes & procedures against BRCGS requirements. Identify areas where your organization needs improvement to meet the standards.
- Establish a Team: Form a dedicated implementation team within your organization. Assign roles & responsibilities to team members to ensure efficient co-ordination & communication throughout the implementation process.
- Training & Awareness: Provide relevant training to employees to ensure they understand BRCGS standards & their role in the implementation process. Create awareness about the importance of food safety & quality throughout the organization.
- Documentation: Develop & update necessary documentation, including policies, procedures & work instructions to align with BRCGS requirements.
- Implementation: Execute the planned actions & changes in processes to meet BRCGS standards. Monitor progress regularly & address any issues that arise.
- Internal Audit: Conduct IA to evaluate effectiveness of implementation & identify any Nonconformity that needs to be addressed.
- Corrective Actions: Implement Corrective Actions for any identified non-conformities to bring your organization into compliances with BRCGS standards
- Verification: Verifying all aspects of BRCGS implementation to be functioning effectively.
- 3P Audit: Scheduling & undergoing an official BRCGS certification audit by an accredited CB. This audit will assess your organization’s compliance with the standard.
- Certification: If your organization meets the BRCGS requirements, you’ll receive certification demonstrating your commitment to food safety & quality.
We offer support for various standards as follows:
BRCGS FOOD SAFETY ISSUE 9
It provides a framework to manage product safety, integrity, legality and quality, and the operational controls for these criteria in the food and food ingredient manufacturing, processing and packing industry. Specifiers, brands, retailers, manufacturers with the BRCGS certification have many food safety benefits such as:
- Widely accepted and specified by many retailers, manufacturers, ingredients companies, food service organizations and raw material processors worldwide as part of their supplier approval process.
- Compliance with a standard that is in line with GFSI 2020 requirements, and covered by recognized IAF accreditation
- Address consumer assurance demands and demonstrate industry best practice by encouraging the development of a product safety culture
- Demonstrate regulatory compliance
- Reduced costs of failure
- Improved business improvement through continual improvement by enhancing root cause analysis and internal audit requirements, as well as access to BRCGS Service Package
– IFS-
FS (International Featured Standards) is a set of globally recognized standards that provide guidelines for the quality and safety of food, products, and services.
The IFS standards are designed to promote transparency, efficiency, and trust between suppliers and retailers.
There are different IFS standards available, but some of the most common ones include:
- IFS Food: This standard focuses on food safety and quality for food processing companies. It sets out requirements for hygiene, management systems, and good manufacturing practices.
- IFS Global Markets Food: Geared towards small and medium-sized enterprises (SMEs) in the food industry, this standard offers a step-by-step approach to help companies gradually improve their food safety practices and eventually attain full IFS Food certification.
- IFS Logistics: Concerned with the storage, distribution, and transportation of food and non-food products, this standard aims to ensure the safety and quality of products during the logistics process.
- IFS Broker: Focused on companies that act as brokers and agents for food and non-food products, this standard establishes requirements for managing product quality and safety within their operations.
- IFS Household and Personal Care: For companies in the household and personal care product industry, this standard covers aspects related to quality, safety, and regulatory compliance.
Here are some ways we can help:
- Training and Education: Offer training programs and workshops to help companies understand the specific requirements of the relevant IFS standard they need to implement. This can include training on food safety practices, quality management systems, and audit preparation.
- Gap Analysis: Conduct a thorough assessment of the company’s current practices and procedures to identify gaps between their existing system and the requirements of the IFS standard.
- Documentation and Procedure Development: Assist in developing and documenting the necessary policies, procedures, and quality management systems to meet the IFS standard’s requirements.
- internal Audits: Conduct internal audits to evaluate the company’s readiness for the official certification audit. This helps identify areas for improvement and ensure compliance with the IFS standard.
- Preparation for Certification Audit: Support the company during the official certification audit by providing guidance and assistance throughout the process.
- Regulatory Compliance: Offer insights into relevant food safety regulations and requirements to ensure that the company aligns its practices with both IFS standards and local regulations.
– GLOBAL GAP-
Global G.A.P. (Good Agricultural Practice) is a private sector-led standard and certification system for agricultural production, particularly focusing on the safety, sustainability, and quality of agricultural products. It was initially developed in Europe to address food safety concerns and has since become a globally recognized standard. The Global G.A.P. standard covers a wide range of agricultural practices, including crop production, livestock production, aquaculture, and other farming activities. It sets criteria for farm management, worker health and safety, animal welfare, environmental protection, and food safety, among other aspects.
Here are some steps to support the implementation process:
- Gap Analysis: Conduct a gap analysis to assess your current agricultural practices and operations against the Global G.A.P. requirements. Identify areas that need improvement to meet the standard.
- Developing a Farm Management System: Establish a farm management system that incorporates Global G.A.P. principles. This may involve creating policies, procedures, and work instructions to guide your agricultural practices.
- Training and Awareness: Train and raise awareness among farm staff and workers about the importance of Global G.A.P. compliance and their roles in implementing and maintaining the standard.
- Documentation: Develop and maintain documentation of your farm’s practices, records, and procedures to demonstrate compliance with Global G.A.P. requirements.
- Risk Assessment and Management: Conduct risk assessments to identify and manage potential risks related to food safety, worker health, and the environment.
- Corrective and Preventive Actions: Implement corrective actions for identified non-conformities and take preventive actions to avoid their recurrence.
- Preparation for Certification: Prepare your farm for Global G.A.P. certification by ensuring compliance with all relevant requirements.
- Third-Party Certification: Engage a reputable certification body to conduct an external audit and grant your farm Global G.A.P. certification upon successful compliance.
- Continual Improvement: Foster a culture of continual improvement to enhance your farm’s compliance with Global G.A.P. standards over time.
- RSPO
- ORGANIC NPOP,
- NOP
- AQUACULTURE AND FISHERIES
- AIB
FSSC
FSSC 22000-
FSSC 22000 (Food Safety System Certification 22000) is a globally recognized food safety management system standard that combines ISO 22000 (food safety management) and PAS 220 (prerequisite programs for food safety). It is designed to ensure food safety throughout the food supply chain, from farm to fork. FSSC 22000 certification demonstrates a company’s commitment to food safety and compliance with international standards.
To support the implementation of FSSC 22000, consider the following steps:
- Conduct a Gap Analysis: Evaluate your current food safety management system against FSSC 22000 requirements to identify areas that need improvement.
- Establish a Food Safety Management System: Develop and document a comprehensive food safety management system based on FSSC 22000 requirements and the specific needs of your organization.
- Training and Awareness: Provide training to employees at all levels to raise awareness of food safety principles and their roles in ensuring compliance.
- Prerequisite Programs (PRPs) and HACCP: Implement PRPs and HACCP principles, as required by the standard, to address food safety controls at various stages of the food supply chain.
- Documentation: Create and maintain documentation of procedures, work instructions, and records related to food safety management.
- Internal Auditing: Conduct internal audits to assess the effectiveness of your food safety management system and identify areas for improvement.
- Certification: We will Engage an accredited certification body to conduct an external audit and grant FSSC 22000 certification upon successful implementation
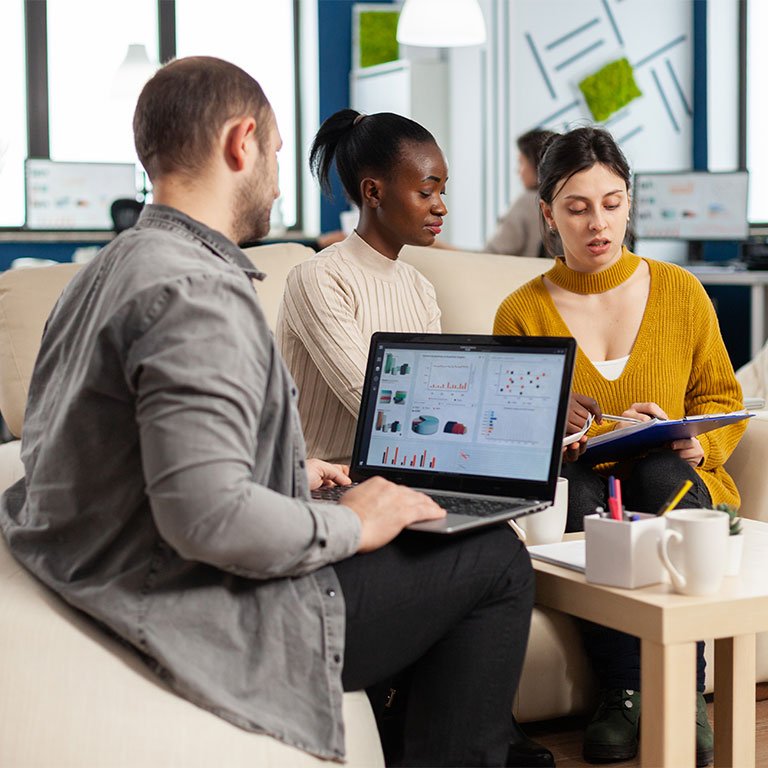
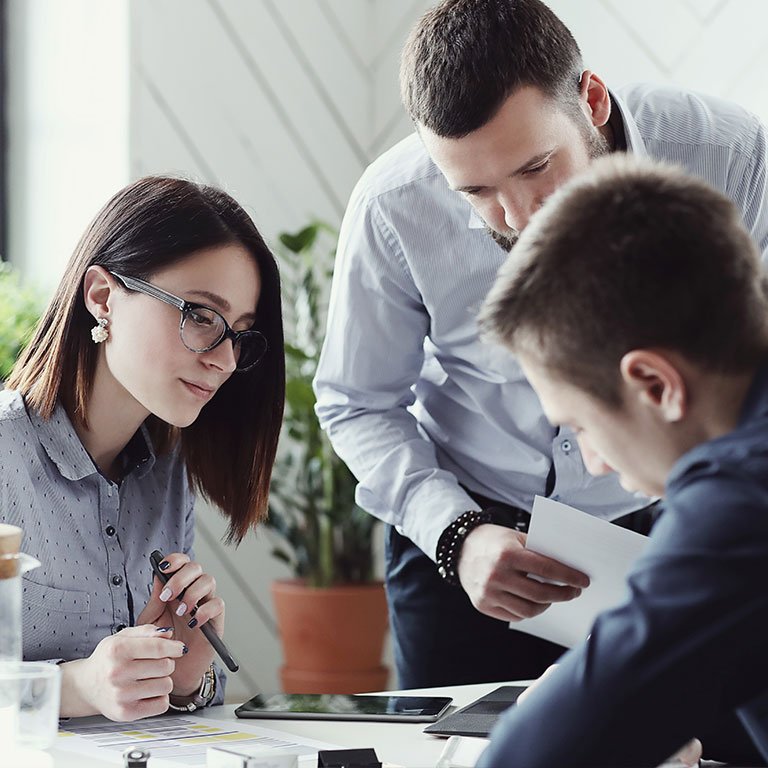

Training was good and helped our team’s better understanding & improved their skills. Also, it was interactive as trainer was flexible to spend more time on crucial topics for our organization.

Emaza Services Private Limited providing best solutions and services to meet current industry requirements The team members of Emaza coordinated and fulfilled all the prerequisites well in advance to complete the task without any hurdles regarding my BRCGS Training.
Thanks to Emaza Founder & CEO Ms. Rohilla Hashhmat

The entire team at Emaza has been very helpful and they are extremely knowledgeable on regulatory compliances and assessments. They have been prompt and deliver before their deadlines. Moreover, they truly work with the company to ensure the success of every project.

The length of support from Emaza officials is phenomenal. Flexibility in choosing courses is of great support for working professional like me. Timely intimation of events, reminders and technical support from Emaza officials are great and well planned. Although the certificates achieved are having my name, however it could not have been possible without support from Emaza staff members specially Vandana Mam. Thank you for your support
Have any Questions? Call us Today!
(123) 222-8888
Third Party Audit
- Retail outlet
- Supply chain
- Farm
Supplier Audit
- URSA
- YUM BRAND
- NESTLE
- PEPSICO
- HEINEKIN
ISO 22000 – Food Safety Management System-
ISO 22000 is an international standard developed by the International Organization for Standardization (ISO) that focuses on food safety management systems. It provides a framework for organizations involved in the food chain to identify and control food safety hazards, ensuring the food products they handle are safe for consumption. ISO 22000 is applicable to all organizations regardless of size, involved in activities such as processing, manufacturing, packaging, storage, transportation, and distribution of food products.
Here are steps to assist in the implementation process:
- Gap Analysis: Conduct a thorough assessment of your current food safety management practices to identify gaps between your existing system and ISO 22000 requirements.
- Establish a Team: Form a dedicated team or appoint a food safety manager to lead the implementation process and coordinate activities.
- Awareness Training: Ensure that all employees are aware of the importance of food safety and their role in adhering to the ISO 22000 requirements.
- HACCP Implementation: Implement Hazard Analysis and Critical Control Points (HACCP) principles, which are essential components of ISO 22000.
- Develop Documentation: Create and maintain necessary documentation, including food safety policies, procedures, work instructions, and records.
- Prerequisite Programs (PRPs) and Operational Prerequisite Programs (oPRPs): Establish and implement PRPs and oPRPs relevant to your organization’s activities.
- Implement CCPs: Identify critical control points in your food production process and implement monitoring and control measures to manage food safety hazards.
- Internal Auditing: Conduct internal audits to assess the effectiveness of your food safety management system and identify areas for improvement.
- Verification and Validation: Ensure the effectiveness and suitability of control measures through verification and validation procedures.
- Continual Improvement: Foster a culture of continuous improvement to enhance your food safety management system over time.
- Seek Third-Party Certification: Support in accredited certification body to conduct a formal audit of your food safety management system and grant ISO 22000 certification upon successful implementation.
ISO 45000 series – Occupational Health & Safety Management System-
ISO 45000 series, can be used as a guideline for saving workers from accidents and occupational diseases. This ensures your organisation by ensuring that performance and safety are not compromised.
Here are steps to assist in the implementation process:
- Gap Analysis: Assess your organization’s current safety management system against requirements of ISO 45000 to identify areas of improvement
- Establish Objectives & Policies: Set clear health & safety objectives, and create policies that align with the standard’s requirement
- Risk Assessment: Identify & evaluate workplace hazards & risks, and establish controls to mitigate them effectively.
- Employee Involvement & Training: Involve employees in implementation process, provide necessary training & communicate the importance of safety.
- Document control: Develop a system to manage & control all relevant documentation related to safety management system.
- Operational Controls: Implement procedures & processes to ensure safe work practices and emergency preparedness.
- Monitoring & Measurement: Set up mechanisms to monitor & measure safety performance, conduct internmal audits, and management reviews.
- Corrective actions: Establish procedures to address nonconformities and take corrective actions when necessary.
- Continual Improvement: Continously review & improve the safety management system based on performance data & feedback
ISO 37001- Anti Bribery Management system
ISO 37001 provides a summary of the best tools for bribery risk management. It also aims to establish a framework for compliance with national anti-bribery laws. Its requirements offer a benchmark for organizations to check or build an anti-bribery management system (ABMS). This certification makes you bring your organization to a better business environment.
Here are steps to assist in the implementation process:
- Risk Assessment: Conduct a thorough risk assessment to identify bribery risk & vulnerabilities within your organization’s operations & business relationships.
- Anti Bribery Policy: Develop & communicate a comprehensive anti-bribery policy that outlines your organization’s stance against bribery & sets clear expectations for employees & business partners.
- Appointing Personnel: Designate a person or a team responsible for overseeing the implementation & maintenance of the anti-bribery management system.
- Training & Communication: Educate employees & relevant stakeholders about anti bribery policies, procedures & importance of complying with ISO 37001 standard.
- Due Diligence: Establish due diligence processes for assessing & selecting business partners, suppliers & other 3rd parties to ensure they meet anti-bribery requirements.
- Financial controls: Implement financial controls & procedures to prevent bribery such as monitoring of expenses,gifts,donations & facilitation of payments.
- Reporting & Investigation: Set up a confidential reporting mechanism for employees to report suspected bribery & establish procedures for investigating and addressing reported incidents.
- Internal Audit: Conduct regular IA to evaluate effectiveness of anti-bribery management system & identify area of improvement.
- Corrective Action: Take appropriate corrective action in response to audit findings or reported incidents to prevent future occurrences of bribery
- Continuous Improvement: Continuously review & improve anti-bribery management system based on performance data & feedback.
ISO 22716- Guidelines on Good Manufacturing Practices (Cosmetics)
ISO 22716 is a standard developed by the International Organization for Standardization (ISO) that provides guidelines for the Good Manufacturing Practices (GMP) of cosmetic products. The full title of the standard is ISO 22716:2007, “Cosmetics – Good Manufacturing Practices (GMP) – Guidelines on Good Manufacturing Practices.” The purpose of ISO 22716 is to ensure that cosmetic products are produced, controlled, stored, and distributed in a consistent, safe, and high-quality manner.
Here’s how we can help:
- Training and Consultancy: We will Offer training sessions and consulting services to educate your staff about ISO 22716 requirements and how to implement them effectively.
- Gap Analysis: Conduct a thorough assessment of the manufacturer’s current practices against the ISO 22716 standard to identify areas that need improvement.
- Documentation: Assist in developing and documenting standard operating procedures (SOPs) and quality management systems in line with ISO 22716 guidelines.
- Facility Design and Maintenance: Provide guidance on designing and maintaining manufacturing facilities to meet the standard’s cleanliness and safety requirements.
- Supplier and Material Control: Help establish procedures for evaluating and selecting suppliers, as well as ensuring the quality of incoming raw materials.
- Auditing and Compliance: Conduct internal audits to assess the manufacturer’s compliance with ISO 22716 and prepare them for external audits.
- Continuous Improvement: Assist in setting up processes for continual improvement and corrective actions, ensuring that the manufacturer maintains compliance over time.
- Regulatory Support: Offer insights into regulatory requirements related to cosmetic products, helping you align with both ISO 22716 and relevant local regulations.
BRCGS PACKAGING ISSUE 6
The BRCGS Packaging Materials Global Standard helps a site or operation to demonstrate they are providing products that are quality assured, legally compliant, and authentic. BRCGS Packaging Materials also helps packaging companies to adapt to changing market forces. Through continuous revisions, BRCGS helps to support in the drive for sustainable and environmental-friendly packaging, changing packaging technology solutions, offline to e-commerce and direct to consumer, plus the control of allergens. Few of the other benefits are as below:
Here’s how we can help:
- Protect your company reputation, brand and image
- Market access as BRCGS certification is the leading global standard recognized by retailers and specifiers
- Improve performance
- Compliance with a standard that is in line with GFSI requirements
- BRCGS STORAGE AND DISTRIBUTION
- BRCGS
- RETAIL BRCGS AGENTS AND BROKER
– SQF-
SQF stands for Safe Quality Food, and it is a globally recognized food safety and quality management system. The SQF program is managed by the Safe Quality Food Institute (SQFI) and is designed to ensure the safety and quality of food products throughout the supply chain.
The SQF program offers various certification levels, including:
Here’s how we can help:
- SQF Food Safety Fundamentals: Designed for small and low-risk food manufacturers, this level provides a basic introduction to food safety management.
- SQF Food Safety Code for Food Manufacturing: Geared towards food manufacturers, this code sets out requirements for food safety and quality management systems.
- SQF Food Safety Code for Primary Production: Targeted at primary producers, such as farms and agricultural operations, this code addresses specific food safety issues in the early stages of the supply chain.
- SQF Food Safety Code for Food Retail and Wholesale: This code is applicable to food retailers and wholesalers, focusing on food safety and quality management in their operations.
- SQF Food Safety Code for Storage and Distribution: Designed for companies involved in the storage and distribution of food products, this code emphasizes safety and quality throughout the distribution process.
Here are some ways we can help:
- Education and Training: Provide training sessions and workshops to familiarize companies with the SQF program and its requirements. This includes educating staff on food safety practices, hazard analysis, and control measures.
- Gap Analysis: Conduct a thorough assessment of the company’s current practices and procedures to identify gaps between their existing system and the requirements of the SQF standard they aim to achieve.
- Documentation and System Development: Assist in developing and documenting the necessary policies, procedures, and quality management systems to meet the specific SQF code requirements.
- Internal Audits: Conduct internal audits to evaluate the company’s readiness for the official certification audit. This helps identify areas for improvement and ensures compliance with the SQF standard.
- Preparation for Certification Audit: Support the company during the official certification audit by providing guidance and assistance throughout the process.
FSSC 24000-
Developed through extensive and open consultation with global stakeholders, the FSSC 24000 Scheme incorporates the internationally recognized, independent standard PAS 24000: Specification for Social Management Systems that includes requirements for social performance. The PAS 24000 standard and the FSSC 24000 Scheme documents are available to download free of charge.
The Scheme can be applied in the manufacturing and processing sector (food and non-food), including their related service provision across the consumer goods industry and their associated supply base.
- SEDEX – SMETA 2 PILLAR & SMETA 4 PILLAR
- EFFCI
- HALAL- The term “halal” refers to what is permissible in Islam, while its opposite, “haram,” refers to what is forbidden. Halal certification is especially important for food and beverages, as Islamic dietary laws outline specific requirements for the sourcing, preparation, and handling of food. However, halal certification can also apply to various other sectors, such as pharmaceuticals, cosmetics, finance, and logistics.
We can support businesses in obtaining and maintaining halal certification through various means:
- Consultancy and Gap Analysis: Offer consultancy services to assess the company’s current practices and identify areas that need improvement to meet halal standards.
- Documentation and Process Development: Assist in developing standard operating procedures (SOPs) and documentation to ensure compliance with halal requirements.
- Training and Education: Conduct training sessions for company personnel to educate them about halal requirements and best practices.
- Auditing and Compliance Support: Prepare the company for the halal certification audit and provide support during the certification process.
- Supplier and Ingredient Verification: Help the company in evaluating suppliers and verifying the halal status of ingredients and raw materials used in their products.
- Regulatory Knowledge: Stay updated on halal regulations and requirements in different markets, providing insights to help the company expand its halal-certified products into various regions.
- KOSHER- Kosher certification is a process by which a certifying agency verifies that a product or establishment complies with Jewish dietary laws and is considered “kosher” for consumption by observant Jews. The term “kosher” refers to food that is prepared and consumed in accordance with Jewish dietary laws, known as “kashrut.” The certification ensures that the food products and processes adhere to these laws, which include guidelines on permitted and forbidden ingredients, the use of dedicated equipment, and supervision during production.
- We can support businesses in obtaining and maintaining kosher certification through various means:
- GMP-
- HACCP
- Pre-audit assessment